Manufacturing
Carbon Activated manufactures activated carbon at plants in Sri Lanka and works with manufacturers in China.
By producing our own media, we can maintain our high quality standards from start to finish.
Activated carbon is produced from coconut shells, wood, coal and other carbonaceous sources. During the activation process, pure carbon is extracted from these materials by a superheating method known as pyrolysis.
Throughout the manufacturing process, samples are collected at various stages and tested for quality in our labs.
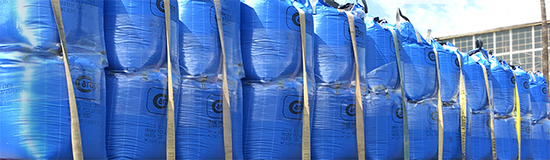
The qualities of our final product depend on:
- the type of raw material used
- the length of the activation and rate of reaction
- the reaction temperature
- the type and concentration of the oxidizing gases
over 300 different applications across a wide variety of industries.
Our quality is guaranteed.
ROTARY KILN | SRI LANKA
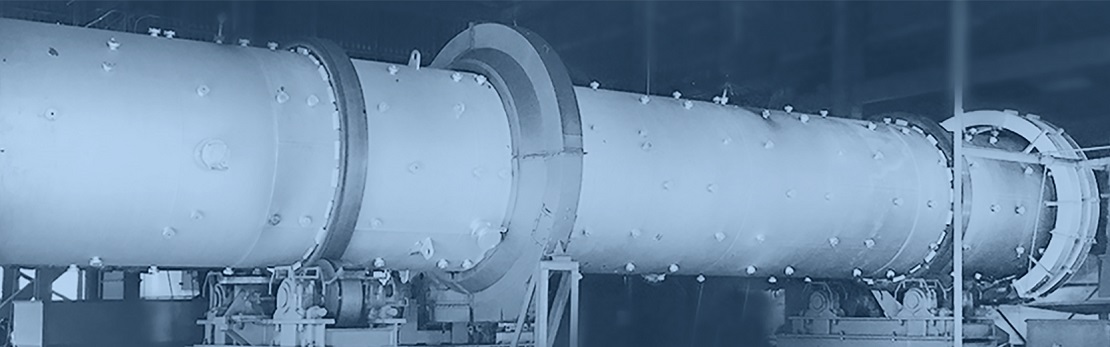
The rotary kiln is a large, slow-rotating cylindrical tube lined with fireclay bricks. The kiln is 20 meters long and 2.4 meters in diameter.
Raw material is continuously fed from a hopper into the rotary kiln which steadily turns the carbonized material inside. As a blower forces air into the kiln, the charcoal reacts with hot steam causing the internal temperature to rise to 900-1100ºC.
The material is activated by hot steam as it moves slowly downwards. The reaction between the steam and charcoal creates pores in the internal surface area, creating more adsorptive spaces. Depending on the temperature and amount of oxygen, this process takes 25-40 minutes.
The activated carbon passes through a screw conveyor with a cooling jacket, reducing the carbon to 200ºC before it reaches the discharging pipe and drops into a cooling kiln. where it is chilled to room temperature, 30-40ºC for several minutes before being fed into a sizing machine, sorted and packed into bulk bags for storage.
MULTIPLE HEARTH KILN | CHINA
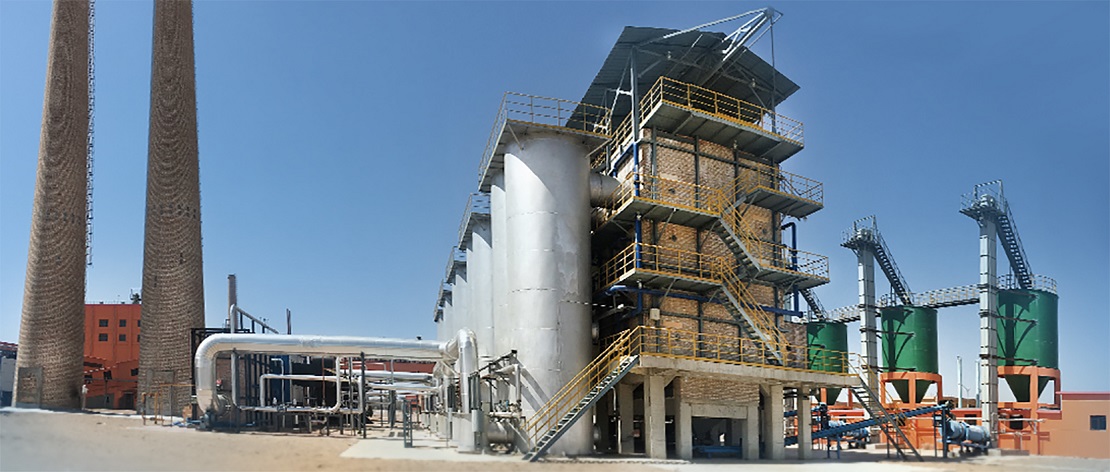
Some of the carbon we source from China are produced from a multiple hearth furnace that manufactures high-grade activated carbon with great efficiency and very little carbon loss.
- The furnace is a large cylindrical carbon steel shell supported on legs of steel 15 meters tall with a diameter of approximately 6 meters.
- The charcoal is carried to the top of the furnace by a bucket elevator.
- Multiple rotating internal hearths carry the materials downward during activation.
- Each hearth has gas burners and steam injectors. The burners and temperature on each hearth are automatically controlled during the process to keep temperatures between 900-1100ºC.
- At the furnace exit, the activated carbon is cooled down via heat exchangers.
- The activated carbon is transported by conveyor to the screening equipment and is bagged from silos to be stored and packaged.